자동차 차체 구조는 크게 2가지다.
먼저 '보디 온 프레임' 방식이 있다. 튼튼한 프레임 위에 엔진과 변속기, 현가장치를 장착하고 그 위에 차체 보디를 얹는 구조다.
국내에서는 기아차 모하비, 쌍용차 G4렉스턴 등이 해당한다.
화물차와 대형 상용차도 같은 방식이다. 하중을 견디는 힘이 크고 노면 상황에 따라 보디가 뒤틀리는 현상이 적다.
대부분 승용차와 미니밴 등이 사용하는 방식은 모노코크(Monocoque) 방식이다.
프레임 없이 차대(chassis) 자체에 엔진과 변속기, 현가장치 등을 장착한다. 애초 높은 기압과 하중에도 견딜 수 있도록 개발한 항공기 제작 기술에서 시작했다.
모노코크 보디는 가볍고 생산원가가 상대적으로 싸다. 다만 시간이 갈수록 엄격해지는 자동차 충돌 강성 기준에 대응해야 한다. 이를 위해 끊임없이 연구와 개발이 반복되고 있다.
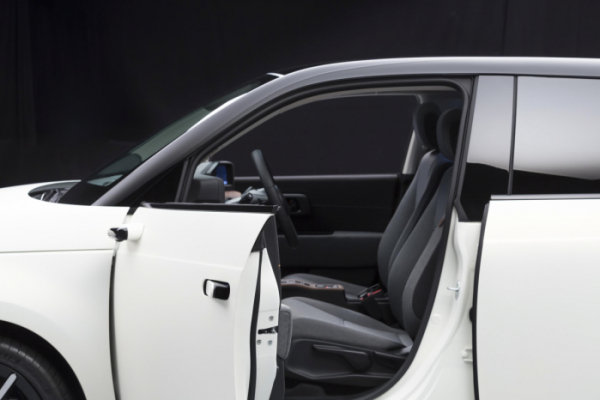
◇충돌 안전기준 강화에 따라 차대 구조 개선=자동차 충돌 안전기준은 점진적으로 기준이 강화되고 있다. 예컨대 1980년대에는 일정 속도 이상으로 고정벽면에 차 전면부 전체가 충돌하는 기준이 유일했다.
이후 차 전면부의 약 45%를 충돌하는, 이른바 오프셋 충돌이 안전기준이 되기도 했다.
차가 견뎌야 하는 부분이 상대적으로 적다 보니 망가짐도 컸다.
이런 상태에서도 안전도를 확보하기 위해 완성차 메이커들이 충돌 상품성 개선에 막대한 예산을 투입하기도 했다.
규제는 더 엄격해졌다. 차 전면부의 25%만 고정벽면에 충돌하는, 이른바 ‘스몰 오버랩’ 테스트가 기준이 됐다. 안전하다고 소문난 자동차 대부분이 이 테스트에서 뭇매를 맞았다.
자동차 안전기준이 까다로운 미국 현지에서 이 방식을 도입했다. 미국에 자동차를 판매하기 위해 여러 완성차 메이커들이 이 기준에 맞춰 차를 생산 중이다.
국내 안전기준 역시 미국의 그것과 큰 틀이 동일하다. "자동차 선진국(미국)의 안전기준을 도입해 자동차 안전도 향상 및 수출 장려를 도모한다"는 게 골자다.
결국, 이를 충족하기 위해 국산차 역시 다양한 연구와 개발, 테스트를 반복 중이다.
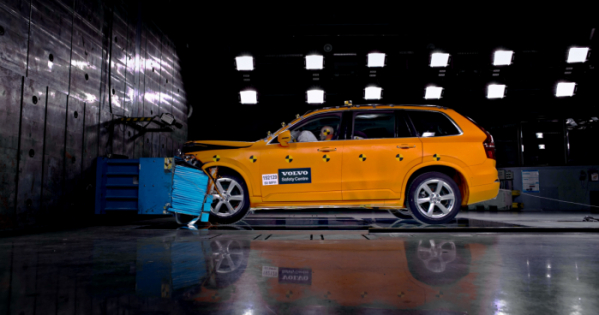
◇차체와 지붕을 연결하는 핵심 기둥=이런 충돌 테스트에서 승객을 보호하는 결정적인 기술이 이른바 필러 강성이다.
필러는 자동차의 차체와 지붕을 연결하는 기둥이다. 앞쪽부터 A, B, C필러라고 부른다.
실내 공간이 넓은, 3열 공간을 갖춘 미니밴과 SUV의 경우 D필러까지 존재하기도 한다.
이런 필러는 단순하게 차의 지붕 강성을 유지하는 차원을 넘어 전면과 측면 충돌 안전성을 확대한다.
예컨대 전면 충돌 때 차 앞면은 충분히 찌그러지게 하지만 운전자와 승객이 타고 있는 실내공간, 이른바 '크럼플 존'은 외부 충격을 끈덕지게 막아내야 한다.
나아가 일정 기준 이상 충돌사고를 겪은 이후에도 운전자와 승객의 탈출이 쉽도록 차 문이 정상적으로 열려야 한다.
이를 지탱하는 힘이 차의 기둥, 즉 필러에서 나온다.
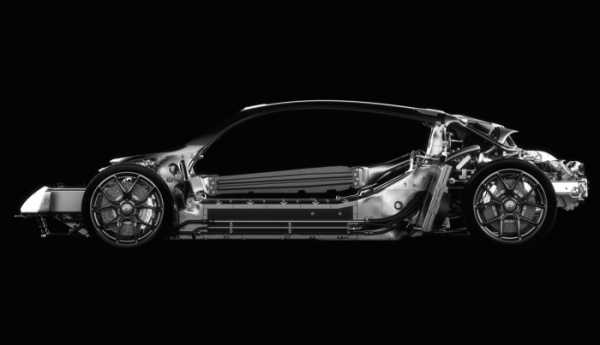
◇전복 사고 대비해 필러 강성 확대 중=반면 모노코크 보디의 경우 외부충격을 차 전체가 흡수하기 때문에 쉽게 구부러진다.
극단적인 충격을 받으면 해당 충격부위를 넘어서 차 전체가 뒤틀어지는 현상이 발생하기도 한다. 중고차를 고를 때 사고 차를 피하려는 이유도 여기에 있다.
필러는 자동차의 지붕과 보디를 연결해 차체를 지탱해주는 기둥을 일컫는다.
승객이 타고 있는 실내의 안전을 고려한 것은 독일 메르세데스-벤츠다.
2차대전이 한창이던 1940년대에 이미 이런 안전 기준을 자체적으로 마련하고 충돌로 인한 충격흡수 및 운전자와 탑승객 보호를 시작했다.
앞 유리를 지탱하면서 운전자와 동반석 승객을 보호하는 A필러는 전체 필러 가운데 가장 중요한 역할을 맡는다.
여러 완성차 메이커들이 초고장력강을 가장 많이 이용하는 곳이 A필러다.
단, 강성에 집중한 나머지 너무 두껍게 필러가 제작되면 전방 시야를 가릴 수 있다는 단점이 존재한다. 결국, 운전자와 동반석 승객의 안전을 최대한 끌어올리되 시야를 가리지 않는 수준의 필러를 뽑아내는 게 관건이다.
1열과 2열을 구분하는 B필러는 측면 충돌에 대비한다. 이 역시 측면 충돌을 막아내는 결정적인 역할을 맡는다. 'B필러 스티프너(보강재)'라고 불리기는 추가 안전장비와 구조물을 덧붙이기도 한다.
이런 필러를 개발하기 위해서는 경량화, 나아가 강성이 필수다.
그 때문에 여러 완성차 메이커들이 섀시(뼈대) 구조를 설계하면서 다양한 필러 구조를 개발하고 있다.
구조역학을 바탕으로 실차 시험을 통해 가장 가볍고 단단한 필러를 개발하는 셈이다. 앞서 개발한 차를 밑그림으로 강성을 확대하기 위해 다양한 실험을 반복한다. 이른바 DOE(Design of Experience)다.
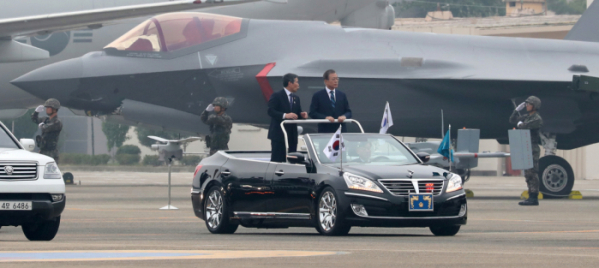
◇탄소섬유 활용해 필러 강성 커져=다양한 경우의 수를 바탕으로 실차로 여러 가지 설계 후보군을 직접 개발해 제작하고 충격 강도를 실험해 최적의 대안을 도출하는 방식이다.
소재도 중요하다. 주철보다 가벼우면서 강성을 확보할 수 있는 '탄소섬유강화플라스틱(CFRP)'이 대표적이다.
주철보다 50%, 알루미늄보다 30% 가벼우면서도 인장강도는 철에 비해 높다는 게 특징이다. 이 소재는 과거에 도어 트림을 포함한 외장재에 주로 쓰였으나 최근에는 단단한 필러 제작을 위해 자주 쓰인다.
조만간 전복 위험에 대비한 자동차 안전기준이 보편화할 예정이다. 필러가 얼마나 단단하냐에 따라 평가 결과가 달라지는 만큼, 지금도 완성차 메이커들은 필러 기술 개발에 밤잠을 줄이고 있다.